VSM: o que é e como construir um em passo a passo?
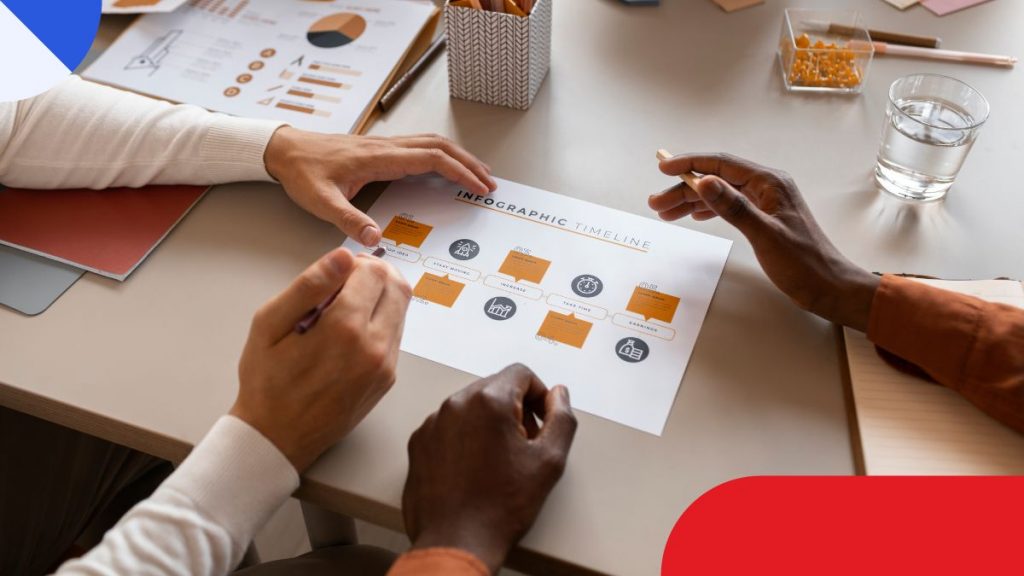
Conteúdo
Em um mundo corporativo onde a eficiência e a produtividade são palavras de ordem, líderes e gestores estão constantemente em busca de métodos que possam aprimorar os processos internos. Nesse cenário, o Mapeamento de Fluxo de Valor (VSM) emerge como uma ferramenta vital que ajuda a identificar não apenas as oportunidades de melhoria, mas também ao criar um vislumbre claro do fluxo de trabalho existente.
Para líderes e gestores que aspiram a uma gestão mais afinada e resultados mais robustos, entender e aplicar o VSM é um passo fundamental na jornada rumo à excelência operacional.
Neste conteúdo, exploraremos o universo do Mapeamento de Fluxo de Valor, desvendando seus princípios, metodologias e, mais importante, como implementá-lo de maneira eficaz em sua organização.
Continue a leitura e confira!

O que é VSM, ou Mapeamento de Fluxo de Valor?
O Mapeamento de Fluxo de Valor (VSM – Value Stream Mapping) é uma técnica originada no Sistema Toyota de Produção, amplamente reconhecida e adotada em diversas indústrias e setores como uma estratégia robusta para melhorar a eficiência dos processos operacionais.
O VSM é uma ferramenta visual que permite aos gestores e líderes de equipe visualizar todo o fluxo de produção, desde a matéria-prima até o produto final nas mãos do cliente, ou, em serviços, desde o início até a entrega do serviço ao cliente.
Dessa forma, ao aplicar o VSM, as organizações conseguem uma visão clara e abrangente de seus processos, o que facilita a identificação de oportunidades de melhoria e a implementação de estratégias mais eficazes para a entrega de valor.
O VSM não é apenas uma ferramenta para identificar problemas, mas uma metodologia que envolve colaboradores na busca por soluções inovadoras e na criação de uma cultura de melhoria contínua.
Alguns dos componentes chaves do VSM são:
- Fluxo de material: representa o caminho que os materiais percorrem desde os fornecedores até o cliente final.
- Fluxo de informação: ilustra como as informações fluem através da organização, garantindo que os materiais se movam eficientemente através do processo de produção.
- Lead time: o tempo total necessário para mover um produto através de todo o fluxo de valor.
- Processos críticos: etapas no fluxo de valor que são vitais para a entrega eficiente do produto ou serviço ao cliente.
Onde surgiu o VSM?
O Mapeamento de Fluxo de Valor tem suas raízes profundamente fincadas no Sistema Toyota de Produção (STP), que é mundialmente reconhecido por suas práticas inovadoras em manufatura e gestão enxuta.
O VSM foi desenvolvido no Japão, mais especificamente dentro da Toyota, na década de 1950, sob a influência de figuras proeminentes como Taiichi Ohno e Shigeo Shingo, que buscavam uma abordagem mais eficiente e enxuta para a produção automotiva.
O Sistema Toyota de Produção emergiu como uma necessidade de otimizar os processos de produção e eliminar desperdícios em um período pós-guerra, onde os recursos eram escassos e a demanda por eficiência era alta. O STP introduziu conceitos revolucionários para a época, como:
- Just-in-Time (JIT): uma estratégia que visa minimizar os níveis de estoque, produzindo itens apenas quando são necessários no processo de produção e na quantidade necessária.
- Jidoka (autonomação): um princípio que habilita as máquinas a detectar e corrigir problemas automaticamente, ou a parar a produção quando ocorrem problemas para evitar a produção de itens defeituosos.
- Kaizen (melhoria contínua): uma filosofia que envolve todos os colaboradores na busca por melhorias contínuas e incrementais nos processos de trabalho.
Embora o VSM tenha sido inicialmente aplicado no setor automotivo, sua aplicabilidade e eficácia foram rapidamente reconhecidas por diversas indústrias e setores ao redor do mundo.
O VSM transcendeu suas origens e foi adaptado para uma variedade de ambientes, incluindo saúde, finanças, e serviços, provando ser uma ferramenta versátil e poderosa para melhorar os processos operacionais e entregar mais valor aos clientes.
Qual a relação entre VSM e Lean Seis Sigma?
O Mapeamento de Fluxo de Valor e o Lean Seis Sigma são duas abordagens poderosas no universo da gestão da qualidade e da melhoria contínua. Ambas as metodologias compartilham um objetivo comum: otimizar processos, eliminar desperdícios e, consequentemente, entregar mais valor ao cliente.
A sinergia entre o VSM e o Lean Seis Sigma envolve:
- Identificação e priorização de projetos: o VSM pode ser utilizado para identificar áreas problemáticas ou de melhoria nos processos, que podem se tornar projetos de melhoria Lean Seis Sigma.
- Análise de processos: o VSM fornece uma visão clara dos processos que podem ser analisados mais profundamente utilizando as ferramentas e técnicas do Lean Seis Sigma.
- Implementação de soluções: o Lean Seis Sigma pode ser utilizado para desenvolver e implementar soluções para os problemas ou oportunidades identificadas através do VSM.
- Monitoramento contínuo: após a implementação de melhorias, o VSM pode ser utilizado novamente para visualizar os impactos das mudanças e identificar novas oportunidades de melhoria.
- Cultura de melhoria contínua: ambas as abordagens promovem uma cultura de melhoria contínua, incentivando as organizações a estar sempre em busca de formas de otimizar seus processos e entregar mais valor aos clientes.
Quais são os benefícios do VSM?
O VSM é uma ferramenta poderosa que oferece uma série de benefícios para as organizações que buscam otimizar seus processos e melhorar a eficiência operacional. Confira a seguir, alguns dos principais benefícios que o Mapeamento de Fluxo de Valor pode proporcionar às empresas:
1. Visibilidade ampliada dos processos
O VSM proporciona uma visão detalhada e abrangente dos processos, facilitando a compreensão de como o trabalho flui por meio da organização.
2. Identificação e eliminação de desperdícios
Ao identificar e eliminar atividades que não agregam valor, as organizações podem reduzir desperdícios e utilizar seus recursos de maneira mais eficiente.
3. Redução de custos
A eliminação de desperdícios e a otimização dos processos frequentemente levam a uma redução significativa dos custos operacionais.
4. Melhoria da qualidade
Ao identificar gargalos e ineficiências, o VSM ajuda a melhorar a qualidade, reduzindo a probabilidade de erros e defeitos.
5. Redução do tempo de ciclo
O VSM ajuda a reduzir os tempos de ciclo, permitindo que os produtos ou serviços sejam entregues mais rapidamente ao cliente.
6. Melhoria na satisfação do cliente
Ao otimizar os processos, as organizações são capazes de entregar produtos e serviços de maior qualidade, aumentando a satisfação do cliente.
7. Fomento à cultura de melhoria contínua
O VSM envolve diversas partes interessadas na análise e melhoria dos processos, promovendo uma cultura de melhoria contínua e engajamento da equipe.
8. Tomada de decisão baseada em dados
A visualização clara dos processos proporcionada pelo VSM permite que os líderes tomem decisões mais informadas e estratégicas.
Quais desperdícios o VSM evita?
Os desperdícios, muitas vezes referenciados na metodologia Lean, são categorizados tradicionalmente em sete tipos, conhecidos pelo acrônimo “TIMWOOD“. Conheça:
1. Transporte
O VSM ajuda a visualizar o fluxo de materiais e informações, permitindo identificar movimentações desnecessárias ou ineficientes. Dessa forma, ajuda a reduzir ou reorganizar os movimentos de materiais e informações para minimizar o transporte desnecessário.
2. Inventário
O VSM destaca áreas onde o inventário excessivo é mantido, seja de materiais, produtos semi-acabados ou produtos acabados. Além disso, ajuda a implementar práticas Just-in-Time e otimizar os níveis de estoque.
3. Movimento
O VSM pode revelar movimentos desnecessários ou ineficientes dentro dos processos de trabalho e reorganizar os espaços de trabalho e processos para minimizar movimentos desnecessários.
4. Espera
O VSM identifica onde ocorrem atrasos e tempos de espera nos processos e ajuda a sincronizar fluxos de trabalho e reduzir tempos de ciclo para minimizar a espera.
5. Sobreprodução
O VSM ajuda a identificar áreas onde a produção excede a demanda do cliente, eliminando a implementação de produção puxada, produzindo apenas o necessário e quando necessário.
6. Sobreprocessamento
O VSM destaca etapas do processo que não agregam valor do ponto de vista do cliente. Dessa forma, ajuda a simplificar processos e eliminar etapas desnecessárias que não contribuem para o valor do produto ou serviço.
7. Defeitos
O VSM também pode ajudar a identificar áreas onde ocorrem defeitos ou erros e implementar práticas de controle de qualidade e prevenção para minimizar defeitos.
8. Desperdício de Talento
Embora não esteja incluído no acrônimo original, o desperdício de talentos é frequentemente considerado o “oitavo desperdício” e refere-se ao subaproveitamento das habilidades e conhecimentos dos colaboradores. Dessa forma, o Mapeamento de Fluxo de Valor ajuda a engajar os colaboradores em atividades de melhoria contínua e aproveitar suas habilidades e conhecimentos para aprimorar os processos.
Como Fazer o Mapeamento de Fluxo de Valor: Passo a Passo
Abaixo, um guia passo a passo para realizar o VSM:
Passo 1: Defina o escopo
Selecione um produto, serviço ou família de produtos para mapear e estabeleça os limites do mapeamento, definindo o ponto de início e de término.
Passo 2: Forme a equipe
Inclua pessoas de diferentes áreas que estejam envolvidas no processo e garanta que todos os membros da equipe tenham um entendimento básico do VSM e seus objetivos.
Passo 3: Mapeamento do estado atual
Obtenha dados sobre o processo, como tempos de ciclo, tempos de espera, qualidade, etc. Utilize símbolos padronizados do VSM para representar visualmente o fluxo de materiais e informações.
Além disso, use o mapa para identificar áreas de desperdício e oportunidades de melhoria.
Passo 4: Análise do Estado Atual
Avalie os desperdícios identificados e determine seu impacto nos processos. Localize os pontos no processo que estão restringindo o fluxo e aumentando os tempos de ciclo.
Passo 5: Desenvolva o estado futuro
Proponha alterações nos processos para eliminar desperdícios e gargalos. Posteriormente, crie um mapa do estado futuro que represente como os processos funcionarão após a implementação das melhorias.
Na sequência, crie um plano para implementar as melhorias, incluindo atividades, responsabilidades e prazos.
Passo 6: Implemente as melhorias
Implemente as melhorias de acordo com o plano desenvolvido e acompanhe o desempenho dos processos e faça ajustes conforme necessário para garantir que os objetivos sejam atingidos.
Passo 7: Mapeamento do estado Ideal
Visualize um estado ideal que represente os processos otimizados ao máximo e desenvolva estratégias para mover os processos do estado futuro para o estado ideal.
Passo 8: Cultive a melhoria contínua
Por fim, realize sessões regulares para revisitar os mapas e identificar novas oportunidades de melhoria e incentive uma mentalidade de melhoria contínua em toda a organização.
Exemplos de quais processos podem ser mapeados usando o VSM
1. Manufatura: Produção de bicicletas
- Processo atual: desde a chegada da matéria-prima até a montagem e expedição das bicicletas.
- Desafios: gargalos na linha de produção, excesso de inventário de peças, e tempos de espera elevados.
- Objetivo do VSM: reduzir o lead time de produção, minimizar o inventário e otimizar a utilização da mão de obra.
2. Saúde: Processo de admissão de pacientes
- Processo atual: desde a chegada do paciente até a sua admissão no hospital.
- Desafios: longos tempos de espera, processamento de documentação e coordenação entre diferentes departamentos.
- Objetivo do VSM: reduzir o tempo de admissão, melhorar a experiência do paciente e otimizar a comunicação entre os departamentos.
3. Serviços financeiros: Processamento de empréstimos
- Processo atual: desde a aplicação do cliente para um empréstimo até a aprovação e desembolso dos fundos.
- Desafios: processamento lento de documentação e atrasos na aprovação.
- Objetivo do VSM: acelerar o tempo de processamento, reduzir erros e melhorar a experiência do cliente.
Como dar o primeiro passo no processo de melhoria?
O primeiro passo para implementar uma cultura de melhoria na sua empresa é contar com um sistema de planejamento estratégico com o objetivo de coletar, armazenar e analisar os resultados dos processos atuais e futuros da companhia.
O acompanhamento integrado da performance corporativa e seus respectivos indicadores é um dos grandes motivos de utilizar um sistema de gestão empresarial. Além do mais, ele permite realizar análises em um só local, agilizando a tomada de decisão e tornando-a mais precisa.
O STRATWS One é um software especialmente desenvolvido para que você crie, analise e compartilhe seus indicadores de desempenho, o que é de grande valia para quem deseja melhorar seus processos.
Veja outras vantagens dessa ferramenta que a fizeram ser escolhida por mais de mil empresas e utilizada por mais de 180 mil colaboradores:
- integrar pessoas, operação e estratégia;
- encontrar oportunidades de melhoria;
- fazer a gestão de reuniões e do portfólio de projetos;
- aumentar a produtividade;
- compartilhar KPIs com agilidade e transparência;
- potencializar a governança corporativa;
- compartilhar informações com agilidade e transparência;
- usar a meritocracia e a gestão à vista para motivar e gerenciar equipes;
- empregar as principais metodologias de planejamento estratégico como BSC, OKR e SWOT;
- gerenciar riscos e analisar cenários;
- facilitar a troca de informação e a comunicação entre departamentos.