Sistema Toyota de Produção: um guia COMPLETO para você
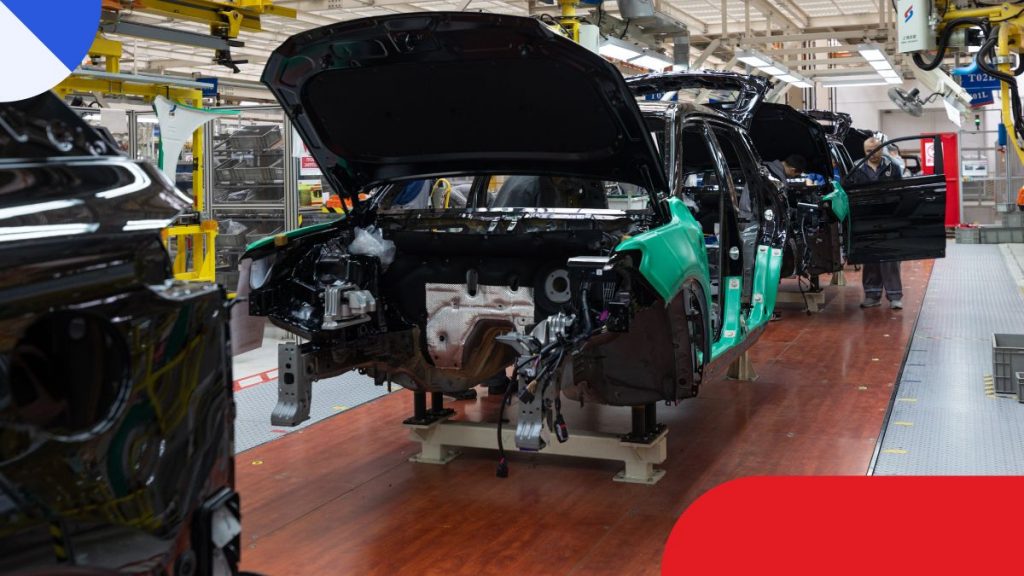
Conteúdo
Em um mundo onde a eficiência e a sustentabilidade se tornaram imperativos empresariais, o Sistema Toyota de Produção (STP) emerge como uma filosofia revolucionária que redefine os padrões de produção e gestão. Originário da gigante automobilística japonesa Toyota, o STP não é apenas uma metodologia de trabalho, mas uma cultura de melhoria contínua e otimização que tem inspirado organizações ao redor do globo.
Este sistema, também conhecido como “Lean Manufacturing“, tem como objetivo principal a criação de valor através da eliminação de desperdícios (muda). Ao focar em processos que agregam valor e simplificar os que não agregam, as empresas podem alcançar uma operação mais enxuta e responsiva.
O resultado? Uma produção mais ágil, custos reduzidos e uma qualidade superior que não apenas satisfaz, mas excede as expectativas dos clientes.
Se está interessado em saber mais sobre o Sistema Toyota de Produção, continue a leitura deste conteúdo e saiba tudo sobre! Confira!
Introdução ao Sistema Toyota de Produção
Nascido no chão de fábrica da Toyota, este sistema transcendeu as fronteiras da indústria automobilística e se tornou um modelo para eficiência operacional em diversas áreas de negócios.
O Sistema Toyota de Produção é mais do que um conjunto de ferramentas; é uma abordagem holística que busca maximizar o valor e minimizar o desperdício — criando produtos de alta qualidade de maneira mais eficiente e econômica.
Além disso, o Sistema Toyota de Produção desafia o status quo, incentivando as organizações a olhar além das práticas tradicionais de produção em massa. Ao invés de empurrar grandes lotes de produção para o próximo estágio do processo, o Sistema Toyota de Produção puxa a produção com base na demanda real do cliente.
Isso não apenas reduz o excesso de estoque, mas também permite uma resposta mais rápida às mudanças na demanda do cliente e melhora a flexibilidade da produção.
Além disso, o Sistema Toyota de Produção é famoso por sua abordagem na resolução de problemas. Em vez de tratar apenas os sintomas dos problemas, o sistema encoraja os trabalhadores a perguntar “por quê?” cinco vezes para chegar à raiz do problema.
Isso leva a soluções mais sustentáveis e a uma melhoria contínua dos processos.
A implementação do Sistema Toyota de Produção pode ser um grande desafio, especialmente em culturas empresariais que estão acostumadas a métodos de trabalho mais tradicionais. No entanto, as recompensas podem ser substanciais.
Empresas que adotam o STP muitas vezes veem melhorias significativas na qualidade, produtividade, eficiência e satisfação do cliente, como falarei mais sobre adiante neste conteúdo.
Pilares do Sistema Toyota de Produção
O Sistema Toyota de Produção é sustentado por dois pilares fundamentais que formam a espinha dorsal de sua filosofia: Just-in-Time (JIT) e Jidoka. Esses conceitos trabalham em conjunto para garantir eficiência e qualidade, eliminando desperdícios e respeitando a inteligência dos trabalhadores.
Just-in-Time: A filosofia de produção sob demanda
O Just-in-Time é uma estratégia que alinha as ordens de produção com a programação de vendas. Em outras palavras, significa produzir exatamente o que é necessário, quando é necessário e na quantidade necessária.
Este pilar do Sistema Toyota de Produção visa reduzir o desperdício resultante de excesso de produção e inventário desnecessário. Ao fazer isso, as empresas podem diminuir os custos de armazenamento, reduzir o capital amarrado em estoque e aumentar a eficiência do fluxo de trabalho.
A implementação bem-sucedida do JIT requer uma compreensão precisa da demanda dos clientes e uma comunicação eficaz ao longo da cadeia de suprimentos. Isso muitas vezes exige uma mudança cultural significativa dentro de uma organização, pois move a empresa de um modelo de “empurrar” para um modelo de “puxar”, onde a produção é impulsionada pela demanda real, não por previsões.
Jidoka: Automação com um toque humano
Jidoka é um conceito que permite que uma máquina pare automaticamente quando ocorre uma anormalidade. Este princípio é muitas vezes traduzido como “automação com um toque humano“.
Em essência, Jidoka dá às máquinas a capacidade de detectar quando um erro ocorre e parar de funcionar, prevenindo a produção de defeitos. Isso permite que os problemas sejam corrigidos imediatamente, garantindo que apenas produtos de alta qualidade avancem no processo de produção.
Além disso, Jidoka tem um aspecto humano importante. Ele empodera os trabalhadores a intervir no processo de produção, parando a linha de montagem se eles identificarem um problema.
Isso não só ajuda a manter a qualidade, mas também envolve os trabalhadores no processo de melhoria contínua, incentivando-os a sugerir maneiras de melhorar a eficiência e resolver problemas de raiz.
Os 7 Desperdícios do Sistema Toyota de Produção
A eliminação de desperdícios é o cerne do Sistema Toyota de Produção. Taiichi Ohno, o arquiteto do STP, identificou sete tipos de desperdícios (muda) que podem ocorrer em qualquer processo de produção.
Reconhecer e eliminar esses desperdícios é fundamental para empresas que buscam otimizar suas operações e melhorar a eficiência. Confira a seguir, os sete tipos de desperdício no Sistema Toyota de Produção:
1. Superprodução
Superprodução é considerada o pior tipo de desperdício porque leva a muitos outros desperdícios. Produzir mais do que é necessário ou antes que seja necessário significa que recursos são utilizados prematuramente, o que pode resultar em excesso de estoque e aumentar os custos de armazenagem.
2. Tempo de espera
Tempo de espera refere-se ao tempo improdutivo que ocorre quando colaboradores ou máquinas estão esperando pelo próximo passo no processo de produção. Isso pode ser causado por gargalos, desequilíbrios na linha de produção ou processos mal sincronizados.
3. Transporte
Transporte desnecessário de materiais pode ser um grande desperdício. Movimentar produtos sem necessidade não agrega valor e aumenta o risco de danos e atrasos, além de ser um custo adicional.
4. Processamento excessivo
Processamento excessivo acontece quando mais trabalho é feito em um produto do que o valor que o cliente requer. Isso pode ser devido a procedimentos desatualizados ou a uma má interpretação das especificações do cliente.
5. Inventário
Estoque excessivo esconde problemas como defeitos de produção, demanda superestimada e tempos de espera prolongados. Além disso, o capital excessivo é amarrado em produtos não vendidos, o que pode afetar a liquidez da empresa.
6. Movimento
Movimentos desnecessários de pessoas ou equipamentos que não agregam valor ao produto podem ser um desperdício. Isso inclui procurar ferramentas, erguer pesos de forma ineficiente e movimentos ergonômicos inadequados.
7. Defeitos
Produtos defeituosos requerem retrabalho ou substituição e podem levar à insatisfação do cliente. A prevenção de defeitos por meio do controle de qualidade e Jidoka é essencial para evitar este tipo de desperdício.
Ferramentas e técnicas do sistema toyota de produção
A implementação eficaz do Sistema Toyota de Produção não seria possível sem um conjunto robusto de ferramentas e técnicas projetadas para identificar e eliminar desperdícios. Estas ferramentas são a base prática que permite às empresas transformar a teoria em resultados tangíveis, otimizando processos e aumentando a eficiência.
Confira a seguir, mais sobre cada uma dessas ferramentas:
#1 Kanban: Simplificando o Fluxo de Trabalho
O Kanban é uma das ferramentas mais emblemáticas do Sistema Toyota de Produção. É um sistema de sinalização visual que controla o fluxo de trabalho e a produção de acordo com a demanda real.
Em um sistema Kanban, um cartão ou sinal é enviado para iniciar a produção ou o movimento de materiais, garantindo que cada etapa do processo seja abastecida com o que precisa, quando precisa e na quantidade exata. Isso ajuda a reduzir o inventário e a superprodução, alinhando a produção com a demanda do cliente.
#2 Kaizen: Melhoria Contínua na Prática
Kaizen, ou melhoria contínua, é o coração pulsante do STP. É a prática de buscar constantemente maneiras de melhorar os processos e eliminar desperdícios.
Kaizen envolve todos os membros da organização, desde a alta administração até os trabalhadores da linha de frente, e encoraja uma cultura onde todos estão empenhados em fazer pequenas mudanças que podem levar a grandes melhorias ao longo do tempo.
#3 5S: Organização e Padronização do Ambiente de Trabalho
O 5S é uma técnica que foca na organização do local de trabalho. Consiste em cinco etapas japonesas: Seiri (Sort), Seiton (Set in order), Seiso (Shine), Seiketsu (Standardize) e Shitsuke (Sustain).
A implementação do 5S ajuda a criar um ambiente de trabalho limpo, ordenado e eficiente, reduzindo o desperdício de movimento e tempo.
#4 Poka-Yoke: Prevenção de Erros
Poka-Yoke é uma técnica de à prova de erros que ajuda a prevenir e eliminar defeitos no processo de produção. Isso é feito por meio do design de dispositivos ou processos que tornam impossível a ocorrência de erros ou que tornam os erros imediatamente evidentes para que possam ser corrigidos.
#5 Heijunka: Nivelamento da Produção
Heijunka é a prática de nivelar a quantidade e o tipo de produção ao longo do tempo. Isso significa produzir em um ritmo constante e evitar flutuações que possam levar a superprodução ou tempo de espera.
Além disso, Heijunka ajuda a criar um fluxo de trabalho mais suave e previsível, o que é essencial para a implementação do Just-in-Time.
#6 Hoshin Kanri: Alinhamento Estratégico
Hoshin Kanri, ou planejamento de políticas, é uma abordagem de gestão estratégica que assegura que as iniciativas de melhoria contínua estejam alinhadas com os objetivos estratégicos da empresa.
Isso garante que todos na organização estejam trabalhando em direção aos mesmos objetivos e que os esforços de melhoria sejam focados onde terão o maior impacto.
#7 A3: Resolução de Problemas e Comunicação
O relatório A3 é uma ferramenta que facilita a resolução sistemática de problemas e a comunicação eficaz. Nomeado após o tamanho de papel internacional A3, este documento ajuda a capturar o processo de resolução de problemas de forma concisa, promovendo a clareza e a compreensão compartilhada.
Benefícios do Sistema Toyota de Produção para a redução de desperdícios
Empresas de diversos setores têm descoberto que, ao abraçar os princípios do STP, elas podem não apenas cortar custos desnecessários, mas também melhorar significativamente a eficiência operacional e a qualidade do produto.
Um dos benefícios mais imediatos do Sistema Toyota de Produção é a sua capacidade de identificar e eliminar os excessos que não agregam valor ao cliente.
Isso é alcançado por meio de uma avaliação meticulosa de cada etapa do processo de produção, com um olhar crítico para a superprodução, o tempo de espera, o transporte desnecessário, o excesso de processamento, o inventário inchado, os movimentos ineficientes e os defeitos.
Ao reduzir esses desperdícios, as empresas podem diminuir os custos de produção e aumentar a sua margem de lucro.
Além disso, o Sistema Toyota de Produção promove uma cultura de melhoria contínua, onde os funcionários em todos os níveis são encorajados a contribuir com ideias para tornar os processos mais eficientes.
Isso não apenas melhora o moral, pois os trabalhadores sentem que têm uma voz ativa na empresa, mas também leva a inovações que podem reduzir ainda mais o desperdício e melhorar a produtividade.
Outro benefício significativo é a melhoria na qualidade do produto. O Sistema Toyota de Produção enfatiza a importância de fazer certo na primeira vez, e o princípio do Jidoka garante que os defeitos sejam detectados e corrigidos no início do processo de produção.
Isso resulta em produtos de maior qualidade e em uma redução na necessidade de retrabalho, o que pode ser um dreno considerável em recursos e tempo.
A implementação do Just-in-Time dentro do Sistema Toyota de Produção também significa que as empresas podem responder mais rapidamente às mudanças na demanda dos clientes.
Isso não só reduz o desperdício associado ao excesso de estoque, mas também permite uma maior flexibilidade e agilidade, tornando a empresa mais competitiva em um mercado em constante mudança.
Desafios e considerações na implementação do Sistema Toyota de Produção
A implementação do Sistema Toyota de Produção não é um processo simples; é uma transformação cultural que exige comprometimento e uma mudança de mentalidade em todos os níveis da organização.
Um dos maiores desafios é a resistência à mudança.
Os funcionários podem estar acostumados a certas práticas de trabalho e podem ver novos métodos como uma ameaça às suas rotinas e, possivelmente, aos seus empregos.
Portanto, é crucial que a gestão demonstre claramente os benefícios do Sistema Toyota de Produção não apenas para a empresa, mas também para os trabalhadores, enfatizando a segurança do emprego através do sucesso da empresa e a oportunidade de participar de um ambiente de trabalho mais eficiente e gratificante.
Outra consideração importante é a necessidade de treinamento contínuo e desenvolvimento de habilidades. O Sistema Toyota de Produção é baseado em princípios e práticas específicas que podem ser muito diferentes dos métodos tradicionais de produção.
Os trabalhadores precisam ser treinados não apenas nas técnicas, mas também na filosofia por trás delas, para que possam entender completamente o valor da melhoria contínua e do pensamento enxuto.
Além disso, a implementação do Sistema Toyota de Produção requer uma abordagem sistemática e disciplinada. Dessa forma, as melhorias devem ser cuidadosamente planejadas, executadas e monitoradas. Isso muitas vezes significa revisar e ajustar os processos de produção, o que pode levar tempo e exigir paciência.
A comunicação também desempenha um papel vital. Para que o Sistema Toyota de Produção funcione efetivamente, deve haver uma comunicação clara e aberta em toda a organização.
Os objetivos e os progressos devem ser compartilhados, e os feedbacks dos colaboradores devem ser encorajados e levados a sério. Isso ajuda a garantir que todos estejam alinhados e comprometidos com a jornada de melhoria contínua.
Próximos passos
O primeiro passo para implementar uma cultura de melhoria na sua empresa é contar com um sistema de planejamento estratégico com o objetivo de coletar, armazenar e analisar os resultados dos processos atuais e futuros da companhia.
O acompanhamento integrado da performance corporativa e seus respectivos indicadores é um dos grandes motivos de utilizar um sistema de gestão empresarial. Além do mais, ele permite realizar análises em um só local, agilizando a tomada de decisão e tornando-a mais precisa.
O STRATWS One é um software especialmente desenvolvido para que você crie, analise e compartilhe seus indicadores de desempenho, o que é de grande valia para quem deseja melhorar seus processos.
Veja outras vantagens dessa ferramenta que a fizeram ser escolhida por mais de mil empresas e utilizada por mais de 180 mil colaboradores:
- integrar pessoas, operação e estratégia;
- encontrar oportunidades de melhoria;
- fazer a gestão de reuniões e do portfólio de projetos;
- aumentar a produtividade;
- compartilhar KPIs com agilidade e transparência;
- potencializar a governança corporativa;
- compartilhar informações com agilidade e transparência;
- usar a meritocracia e a gestão à vista para motivar e gerenciar equipes;
- empregar as principais metodologias de planejamento estratégico como BSC, OKR e SWOT;
- gerenciar riscos e analisar cenários;
- facilitar a troca de informação e a comunicação entre departamentos.